下一代干式快速接头功能创新的球阀设计,使液体输送在制药应用更高效
Next-generation Dry Disconnect Coupling feature an innovative ball-valve design that enables the optimization of liquid transfer in pharmaceutical application.
- by David Gibble, Product Manager, Chemical & Industrial Business Unit, for OPW Engineered Systems
The keys to establishing a successful pharmaceutical-manufacturing operation may be as basic as adhering to a pair of familiar, time-honored clichés: “better safe than sorry” and “time is money.” Sure, taking a pharmaceutical end product from the R&D lab to the hands of the consumer isn’t easy, but the process can be optimized if the raw materials and end products that are handled—many of which necessarily are, or must contain, volatile or hazardous compounds—are done so safely while simultaneously following a streamlined manufacturing schedule that can maximize the returns from profitable patent windows.
Finding that nirvana in pharmaceutical manufacturing space, however, requires a lot of specific steps to be completed succinctly and reliably. Take the transfer of liquids in the process. There are many transfer points, starting when raw materials arrive at the manufacturing facility via truck or railcar, then through the various piping and switching manifolds that facilitate the storage, dosing, blending, mixing, tote-filing, bottling, and packaging stages that make up the many links in the production and supply chain.
Throughout the liquid-transfer processes, pharmaceutical manufacturers are hoping to optimize two critical things: the safety of production personnel and the environment and the time needed to complete the manufacturing process.
Ensuring personal and environmental safety is important because many of the raw materials used in pharmaceutical manufacture can be volatile, hazardous, or corrosive—compounds such as toluene, dichloromethane, ammonia, different slurries, and Syltherm, for example—so they must be properly contained. After all, there is a common saying among pharmaceutical manufacturers: “every pharmaceutical plant is nothing more than a chemical plant.”
Additionally, preventing spills or leaks is vital because any that occur, besides being dangerous on various levels, have the potential to interrupt the production schedule, which not only delays product completion, but can also lead to the loss of high-value, expensive ingredients and the incurrence of prohibitive cleanup costs.
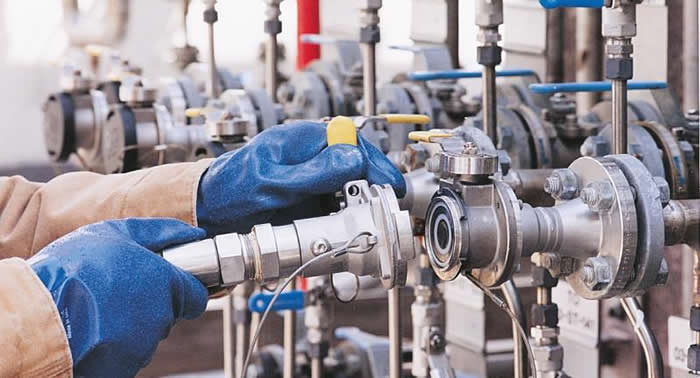
Pharmaceutical manufacturing requires the precise handling and dosing of both high-value and hazardous raw materials and end products, necessitating the need for dry disconnect coupling technology that provides a consistent flow rate with little chance of product spills or leaks. The Epsilon Dry Disconnect Coupling from OPW Engineered Systems meets those needs thanks to its innovative ball-valve design.
Pharmaceutical manufacturing requires the precise handling and dosing of both high-value and hazardous raw materials and end products, necessitating the need for dry disconnect coupling technology that provides a consistent flow rate with little chance of product spills or leaks. The Epsilon Dry Disconnect Coupling from OPW Engineered Systems meets those needs thanks to its innovative ball-valve design.
OPW Epsilon low-spill dry disconnect coupling Video
Taking the Plunge
Over the years, a certain type of technology has risen to the fore when pharmaceutical manufacturers are looking for a dry disconnect technology to implement with the various hoses that will be attached to trucks, railcars, manifolds, and pipes during the liquid-transfer process. This technology is referred to as either a “bayonet-and-plunger” or “poppet” style coupler.
The bayonet-and-plunger dry disconnect coupler technology has gained acceptance because its design and operation possesses a number of benefits for the user. Most important, there is relatively little fluid loss when the coupler is disconnected, as little as 0.5 milliliter (ml) of fluid, or the equivalent of 1/10th of a teaspoon, which is approximately 0.017 of an ounce. They are also generally equipped with safety locks that prevent the coupler from opening accidentally as fluid is flowing through it.
Most brands of bayonet-and-plunger couplers are lightweight and easy to maneuver, which eliminates undo operational stress and strain on the operator. Their low cost also makes them attractive to manufacturers who are looking to streamline capital costs and protect the operation’s bottom line.
With all that being said, bayonet-and-plunger couplers do have a number of negative operational characteristics that prohibit them from being the absolute best dry disconnect coupler technology choice in pharmaceutical-manufacturing applications. First, while an extremely small amount of fluid may be lost during disconnection, there are other coupler technologies that will lose lesser amounts of fluid.
From an operational standpoint, the biggest shortfall of bayonet-and-plunger couplers is their design, which puts a number of internal parts in direct contact with the fluid flow. Any type of flow-rate restriction will negatively affect the production process. For example, if an engineer specifies a 2” line and a bayonet-and-plunger coupler with a 2” I.D. is installed, the flow rate will actually be less than what is to be expected from a free-flow 2” line because the liquid will have to work its way around the coupler parts that it comes into contact with. This may also necessitate the need for a larger-than-necessary 2.5” and 3” coupler.
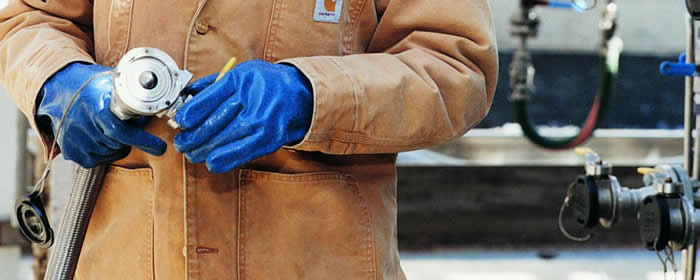
Additionally, the bayonet-and-plunger coupler’s internal components, things such as springs, guides and poppets, can also create areas where the liquid can collect and hide, which makes it difficult to clean the lines and maintain a sanitary pumping environment.
Bayonet-and-plunger couplers can be at a disadvantage when manufacturers choose to incorporate a closed-loop fluid-transfer system, which is becoming more popular in pharmaceutical-manufacture processes. The drawback is that in a closed-loop system there may be numerous valves deployed, meaning that at some point the closing of two valves will leave product trapped in the hose between the closed valves. The pressure that is created when the downstream valve is subsequently opened has the potential to damage the coupler ahead of it, which can lead to leaks and product spills.
Lastly, bayonet-and-plunger couplers are harder to repair or maintain inline because of the number of parts they contain. In fact, many bayonet-and-plunger suppliers require the coupler to be removed and returned to the manufacturer for repairs. If the coupler can be repaired in the field, the number of steps required and number of parts to consider can make it difficult or confusing for the maintenance technician.

Caption: The unique ball-valve operation of the OPW Epsilon Dry Disconnect Coupling allows a convex ball to seat with a concave ball when the valve is opened, in the process creating a straight-through flow path with no cavities or crevices where product can rest. Conversely, the design of traditional poppet-style dry disconnects allows a small amount of liquid to be trapped during disconnection, which can lead to spills that can be harmful to site personnel and the environment.
Caption: The unique ball-valve operation of the OPW Epsilon Dry Disconnect Coupling allows a convex ball to seat with a concave ball when the valve is opened, in the process creating a straight-through flow path with no cavities or crevices where product can rest. Conversely, the design of traditional poppet-style dry disconnects allows a small amount of liquid to be trapped during disconnection, which can lead to spills that can be harmful to site personnel and the environment.
A Better Solution
While bayonet-and-plunger dry disconnect couplers have performed admirably in pharmaceutical-manufacturing applications over the years, a new dry disconnect coupler technology has emerged that is able to overcome the shortcomings found in poppet-style couplers. This next-generation coupler technology operates via an innovative double-ball-valve design, rather than bayonet-and-plunger.
The design features a convex ball that rests in a concave ball, resulting in the elimination of any cavity between the mating halves and guaranteeing that no residual fluid will be trapped there, lowering the risk of spills and giving the liquid virtually no place to collect or hide, which eases cleaning and raises the level of sanitary operation. Specifically, upon disconnection, there will be less than 0.5 ml of fluid left on the face seal of the coupler, an amount that is less than one-quarter of a teardrop.
The ball-valve design also incorporates multiple safety interlocks that allow the valve to open and close only through a deliberate action by the user. This prevents any accidental opening of the valve, which lowers the risk of unintentional spills and catastrophic chemical releases. This is not only critical when transferring raw materials from large storage vessels, but also during the numerous tote-filling operations that are a staple of pharmaceutical manufacture. This constant on-and-off filling of smaller-capacity vessels can put undo strain on the couplers, but the ball-valve design and method of operation nullify the harmful effects.
Another way these new couplers can help improve safety is found in the fact that the coupler’s face seal—which is available in FDA-compliant TFM or PDA—is more resistant to abrasion than competitive technologies. Any grit, dirt, or particulates that get on the seal have the potential to leave scratches, with the scratches capable of creating leak paths. Because the face seals have a higher level of abrasion resistance, the chance of scratch-induced leak paths being formed is minimized.
The ball-valve design also creates an unrestricted flow path, which minimizes pressure drop and results in less than 1 psi in pressure drop at a flow rate of 150 gallons per minute (568 liters per minute). In other words, a liquid-transfer system that calls for a 2” hose can utilize a 2” ball-valve coupler model without any reduction or restriction to the required flow rate.
The final benefit of the new ball-valve coupler when compared to its bayonet-and-plunger cousins is its ease of maintenance. Because it has fewer parts than competitive technologies, the ball-valve coupler can be repaired on-site very easily, with no need to return the coupler to the manufacturer or in-the-field repair personnel to battle with complicated and confusing repair or maintenance instructions.
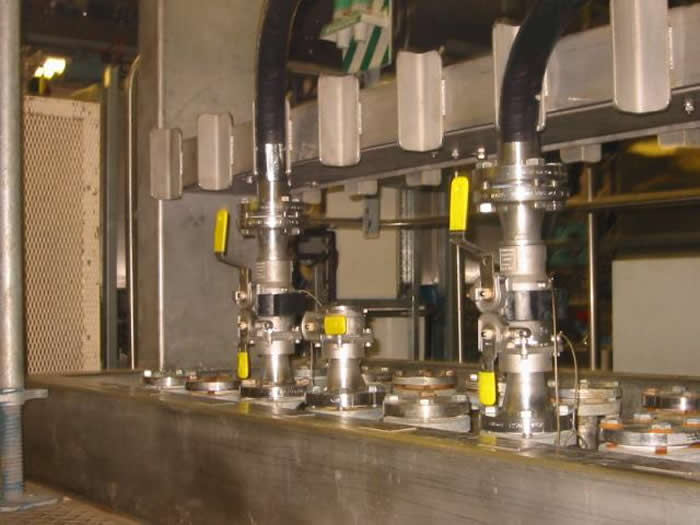
The unrestricted flow path of the OPW Epsilon Dry Disconnect Coupling enables pharmaceutical manufacturers to experience optimized loading and unloading times.
Conclusion
Achieving safe operation and cost-effectiveness is a day-to-day challenge for pharmaceutical manufacturers, especially when the raw materials used are both hazardous and expensive. With many production operations requiring large tank farms and the transfer of thousands of gallons of raw materials and end products on a daily basis, the type of dry disconnect coupler used, and the technology’s ability to optimize safety and cost is a critical concern.
While legacy coupler technologies have proven to be effective in meeting the basic needs of liquid transfer, the process can be taken to the next level with the use of a next-generation technology like the ball-valve dry disconnect coupler. This technology provides the operational advantages—reliable, safe, and leak-free product containment; full-flow capability; regulatory compliance; and ease of repair and maintenance—that will enable pharmaceutical manufacturers to meet their needs regarding safety and timely production.
About the Author
David Gibble is Product Manager, Chemical & Industrial Business Unit, for OPW Engineered Systems, part of Dover Corporation’s OPW division. He can be reached at (800) 547-9393 or dgibble@opw-es.com. OPW is the global leader in fully integrated fluid-handling, management, monitoring, and control solutions for the safe and efficient handling of critical petroleum-derived fluids from the refinery to the commercial and retail points of consumption, including loading systems, rail and transport tank-truck equipment, tank-gauging equipment, and automated fuel-management systems, valves and fittings, underground and aboveground storage-tank equipment, spill containers, overfill-prevention devices, secondary-containment sumps and flexible piping, fuel-dispensing products, including swivels, breakaways, industrial and automatic dispensing nozzles for vapor recovery, gasoline, diesel and alternative fuels, and clean energy fueling nozzles and accessories for LPG, Hydrogen and CNG. OPW also manufactures automated vehicle wash systems. OPW has 1,650+ employees with manufacturing operations in North America, Europe, Brazil, China, and India and sales offices around the world. OPW is an operating company within the Fluids segment of Dover Corporation (NYSE: DOV).
Epsilon适用于危险性流体疏松的压降-小的干式快换接头
Epsilon低泄露接头系统
EPSILON是一种经过精密安全设计的基于双球阀系统的低泄露接头。除了拥有球形阀设计所具备的共有优点之外,EPSILON接头还为管路连接中的流体提供一条自由流动通道,并且在接头连通时具有双重锁紧功能,增加系统的可靠性。EPSILON接头系统是为了用于避免化学制品的泄漏和减少挥发性有机化合物(VOC)的散逸性排放,尤其是在过程设备中和槽车装卸过程中。EPSILON化学制品存储系统可以为你的工厂在化学制品的输送过程提供更适应的工艺流程,如改善人员的安全性和降低环境污染的风险,并为您减少总的资金花费和降低运行成本。
EPSILON快换接头特点
- 提供3/4”, 1”, 1-1/2”, 2” 和3”规格
- 提供不锈钢和Hastelloy材质
- 适用的接口标准为ANSI美国标准和DIN欧洲标准。
- 符合FDA标准的密封材料,TFM
Next generation PTFE with best combination of temperature ranging from -22°F (-30°C) to 450°F (230°C), sealing, and sliding characteristics.
- 设计的-大工作压力为435 psi(30Bar),-高温度可达450°F(230°C)
- 弹簧操动并加载的TFM或PFA U型杯密封结构
A spring-energized stem and face and flange seal provide initial sealing. The spring supplies all the load required for sealing when the media pressure is too low to fully actuate the lips of the seal. Testing confirms the low spillage and emission specifications are still achieved after 2,000 cycles.
- 聚氨酯防尘罩或不锈钢承压盖帽
Used to protect the ball from damage and debris when coupling is closed and disconnected.
- 外螺纹和内螺纹凸耳/法兰联接面
Ramped lug and flange interfaces are first aligned and then connected with a push, followed by a quarter (90°) turn. This “instant” connection method is done by hand without tools in order to create compression on the critical interface seal.
- 独立、多级安全联锁装置
EPSILON technology involves five independent and redundant mechanical interlocks. They require deliberate sequential action by users, thereby eliminating unintentional spills and catastrophic chemical releases that threaten worker safety and the environment.
- 经多家国际机构批准可用于各种承受压力的用途
|